Artificial Intelligence in Industry 4.0 enables companies to manufacture, enhance and distribute their products in revolutionized new ways. Welcome to the era of so-called dark factories!
Manufacturers are integrating new technologies into their manufacturing facilities and operations, including artificial intelligence and its subdomain machine learning, as well as the Internet of Things (IoT), cloud computing, and analytics. In addition to making production more agile and flexible, Industry 4.0 enables the capture of variables and parameters that have been hidden until now in production operations. This is exactly what makes factories “smart,” providing unprecedented scope and granular control over the entire manufacturing operation.
AI vs Machine Learning
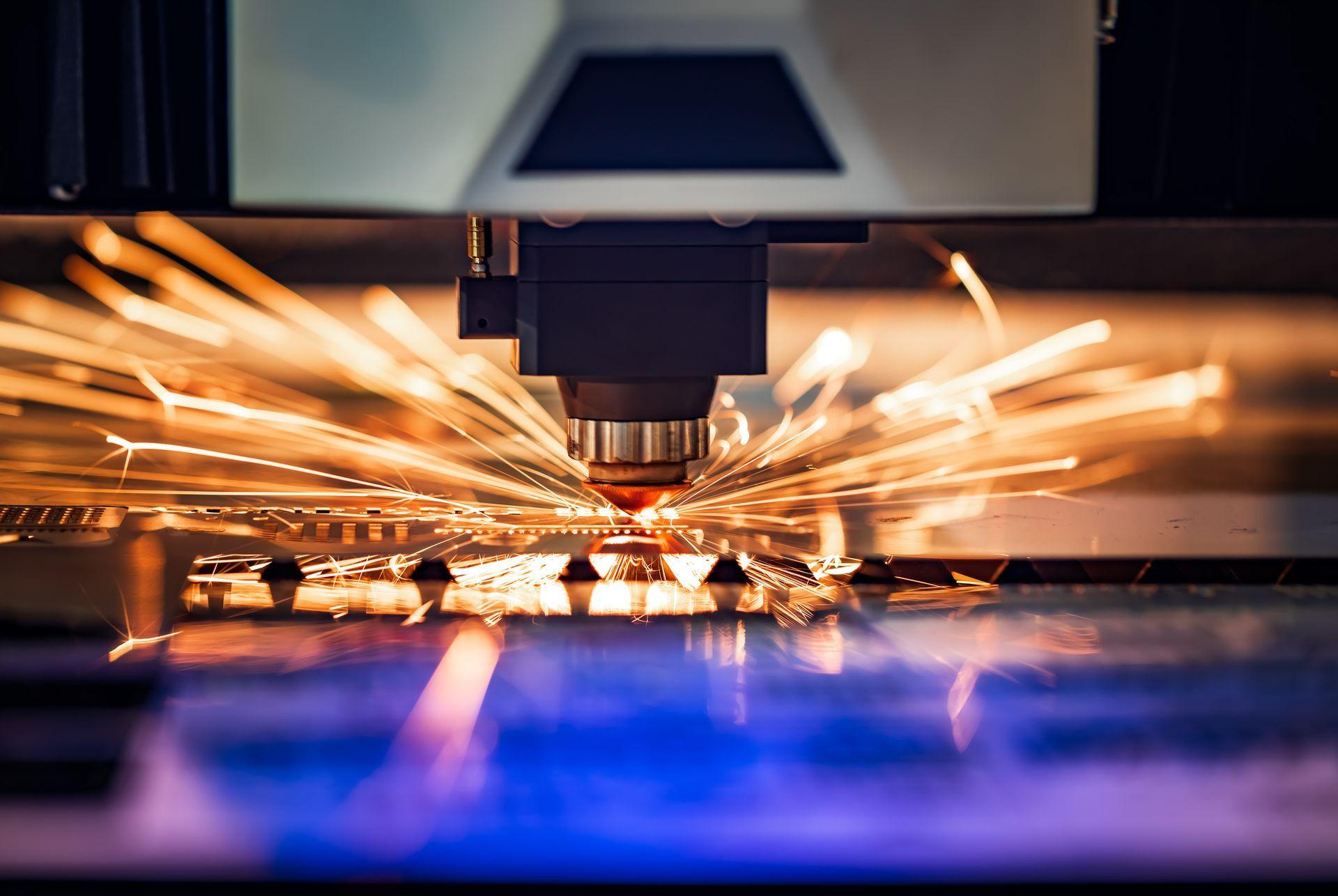
Before we begin to explore how artificial intelligence is shaping Industry 4.0, it would be practical to assess the fields of artificial intelligence and machine learning together. Because in the later parts of this article, for the comfort and experience of you, dear readers, the term AI is also used to describe machine learning algorithms in multiple places. AI and Machine Learning are intimately linked, but they’re not the same. Machine Learning is a form of AI.
Artificial Intelligence (AI) is the ability of a computer system to mimic human cognitive functions, such as learning and decision making. A computer system uses math and logic to simulate the learning processes that humans use when learning from new information and forming decisions.
Machine Learning (ML) uses data-driven mathematical models to help a machine learn without being told explicitly. This allows a computer system to learn independently and improve due to experience.
“Intelligent systems” employ AI to think like a person and execute tasks without direct supervision. Computer systems acquire their intelligence in two ways: through Machine Learning or Natural Language Processing (NLP).
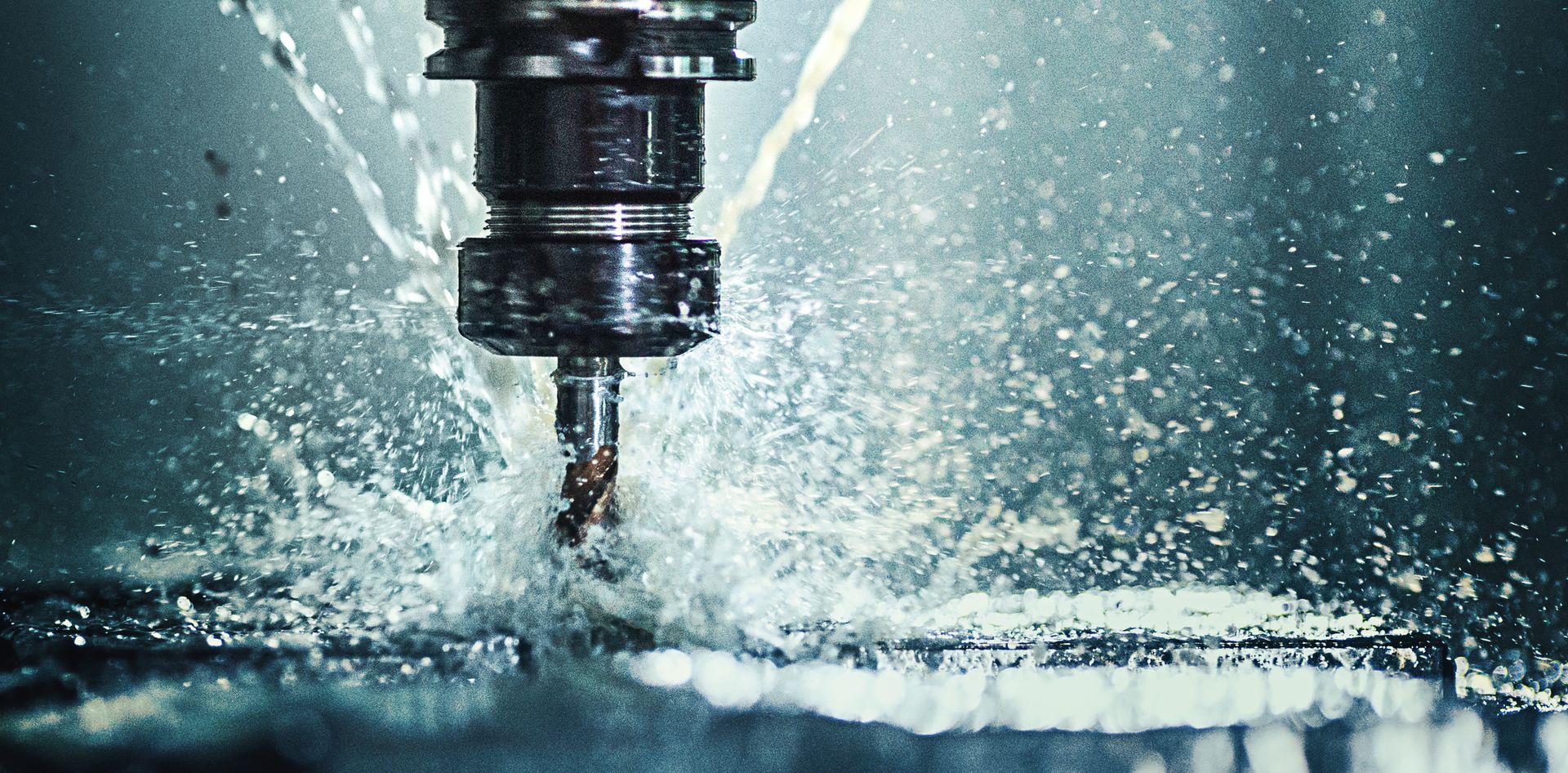
AI with Machine Learning
Artificial Intelligence and machine learning provide significant advantages for businesses in almost every sector. Manufacturers utilize Artificial Intelligence in Industry 4.0 and Machine Learning to improve their operations more than before.
With AI and Machine Learning, companies have developed innovative ways to profit from data in unstructured and semi-structured forms. Through process automation, companies become more efficient, which lowers costs while freeing up time and resources for other priorities. Machine Learning is becoming increasingly sophisticated, and AI is becoming more accessible—both for good. Improved data integrity and AI to reduce human error combine to result in better decisions based on improved data.
AI as a tool, as it always should be
The problem with “buzzwords” like artificial intelligence and Industry 4.0 lies in their mind-blowing potential. Organizations must consider today and the future when making decisions. Still, when it comes to technology investment, the project that saves the day (-to-day operations) is the one that has a tangible advantage to the context and organization it is applied.
AI is one of the most talked-about technologies. You can guess the disinformation and dreaminess revolve around it. When we separate ideas from tools that deliver short- and long-term results, we can better examine how Artificial Intelligence is currently already changing manufacturing and has already kicked off Industry 4.0. The lights will stay on for a while in factories, which may be the best for us all.
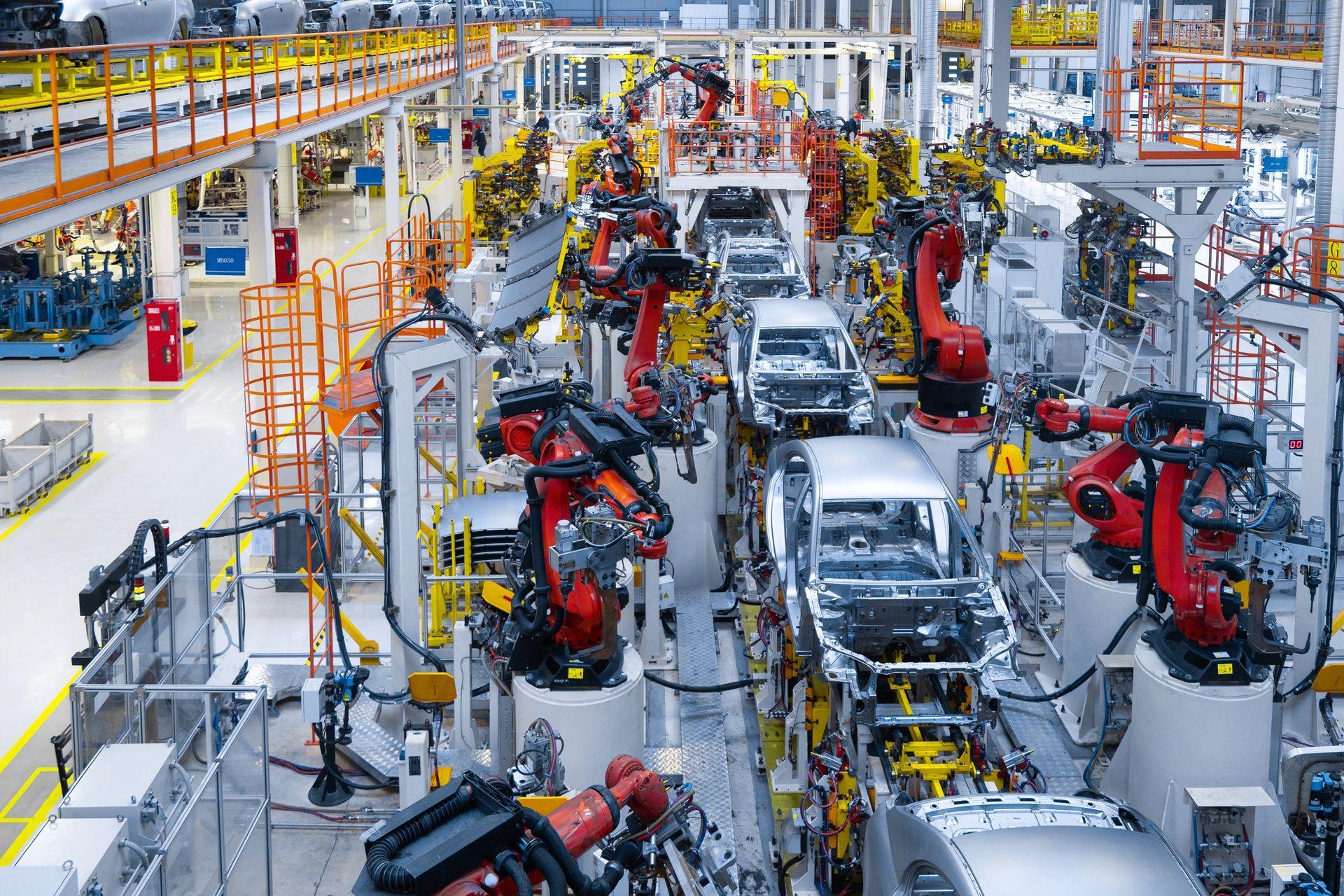
Artificial Intelligence in Industry 4.0
Manufacturers utilize AI and Machine Learning to fully take advantage of the massive amounts of data generated on the factories, business units, partners, and third-party sources. By generating insights, Artificial Intelligence in Industry 4.0 provide visibility, predictability, and automation to manufacturing processes and business procedures.
Artificial Intelligence in Industry 4.0 has several tangible benefits for manufacturing operations. The first and foremost is error reduction. Well-trained Machine Learning algorithms outperform humans in terms of perfection and efficiency on error-prone tasks for humans. This reduces the amount of time and resources wasted on inefficient operations, and faulty products-which translates to cost reduction and revenue growth. And these great benefits are enabled with only a few AI applications in manufacturing nowadays.
· Predictive analytics
Predictive Analytics is a form of advanced analytics that draws conclusions about future events based on prior data, statistical modeling, data mining methods, and Machine Learning, a subset of Artificial Intelligence. Manufacturers use Predictive Analytics to find patterns in their data to identify faults and anomalies in their operations.
· Predictive maintenance
Predictive Maintenance is an AI-based, proactive maintenance technique that monitors an asset’s condition, status, and performance. Predictive maintenance aims to reduce costly and unscheduled failures by allowing manufacturers to plan maintenance around their manufacturing schedule. Machine Learning algorithms predict the errors that will occur on the production line, in a sense, ensuring that the malfunctions are eliminated before they even occur.
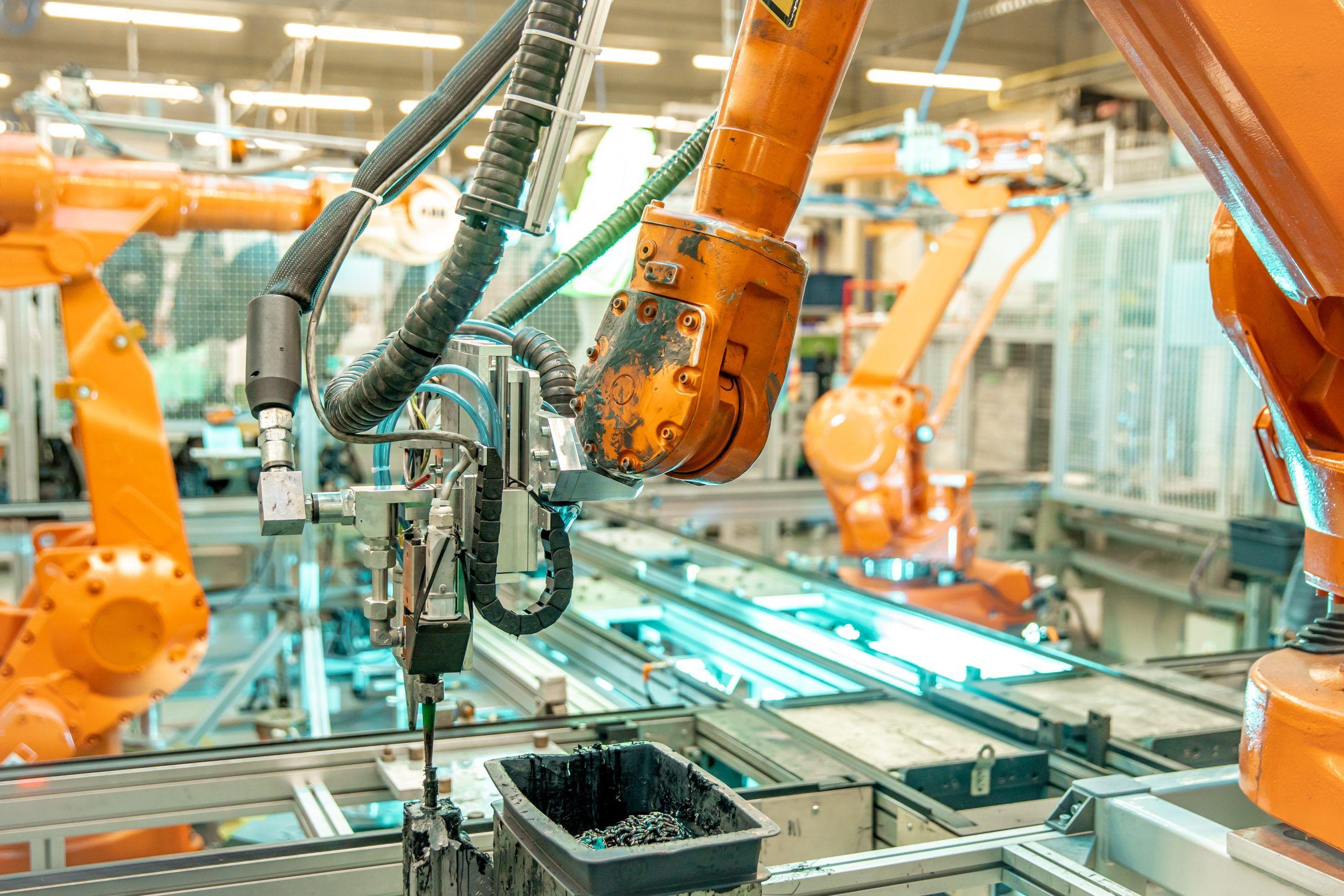
· Industrial robotics
Industrial robots have already been in use for more than 50 years, but they have recently shed their reputation as coldly competing against human employees and supplanting them with ruthless efficiency to amiable helpers who can make line workers’ lives easier rather than stealing their jobs. Artificial intelligence help robots become more accurate and dependable, as well as allow for more sophisticated mobility. Perhaps most significantly, Artificial Intelligence in Industry 4.0 may significantly reduce the programming and engineering work required to develop and implement industrial automation.
· Computer vision
The majority of industrial Computer Vision applications focus on visual inspections. Artificial Intelligence has two obvious benefits over humans when it comes to visual inspection: Swiftness and precision. A Computer Vision system with cameras that have greater sensitivity than the human eye and complemented by AI can discover tiny flaws straightaway that human inspectors would overlook.
· Inventory management
Artificial Intelligence in Industry 4.0 reduces inventory-related expenses in various ways, from optimizing what is kept on hand to anticipating gaps before they arise. AI’s ability to process massive amounts of data and discover hidden patterns makes it an ideal tool for inventory management. Amazon is the most well-known company that has used AI for inventory management.
There are several more instances of artificial intelligence in Industry 4.0, including sustainability, waste reduction, and supply chain management. As computational resources become less expensive and domain expertise proliferates, the number of AI manufacturing applications will undoubtedly rise.
Smart factory simplified
The most common characteristics of today’s smart factories are interconnectivity and data-driven decision-making. Embedded sensors and connected machinery generate Big Data for manufacturing companies. This data contains critical knowledge on almost every facet of the operation. Artificial Intelligence in Industry 4.0 analyzes it for prior patterns and suggests methods for manufacturers to improve. AI also can use data from other areas of the company and its ecosystem of suppliers and dealers to create more detailed insights.
Smart factories are built on interconnectivity. Real-time data gathered from sensors, machines, and employees on the production floor may be consumed and utilized immediately by other factory assets as well as shared across other components of the software stack, including Enterprise Resource Planning (ERP) and other Business Management systems.
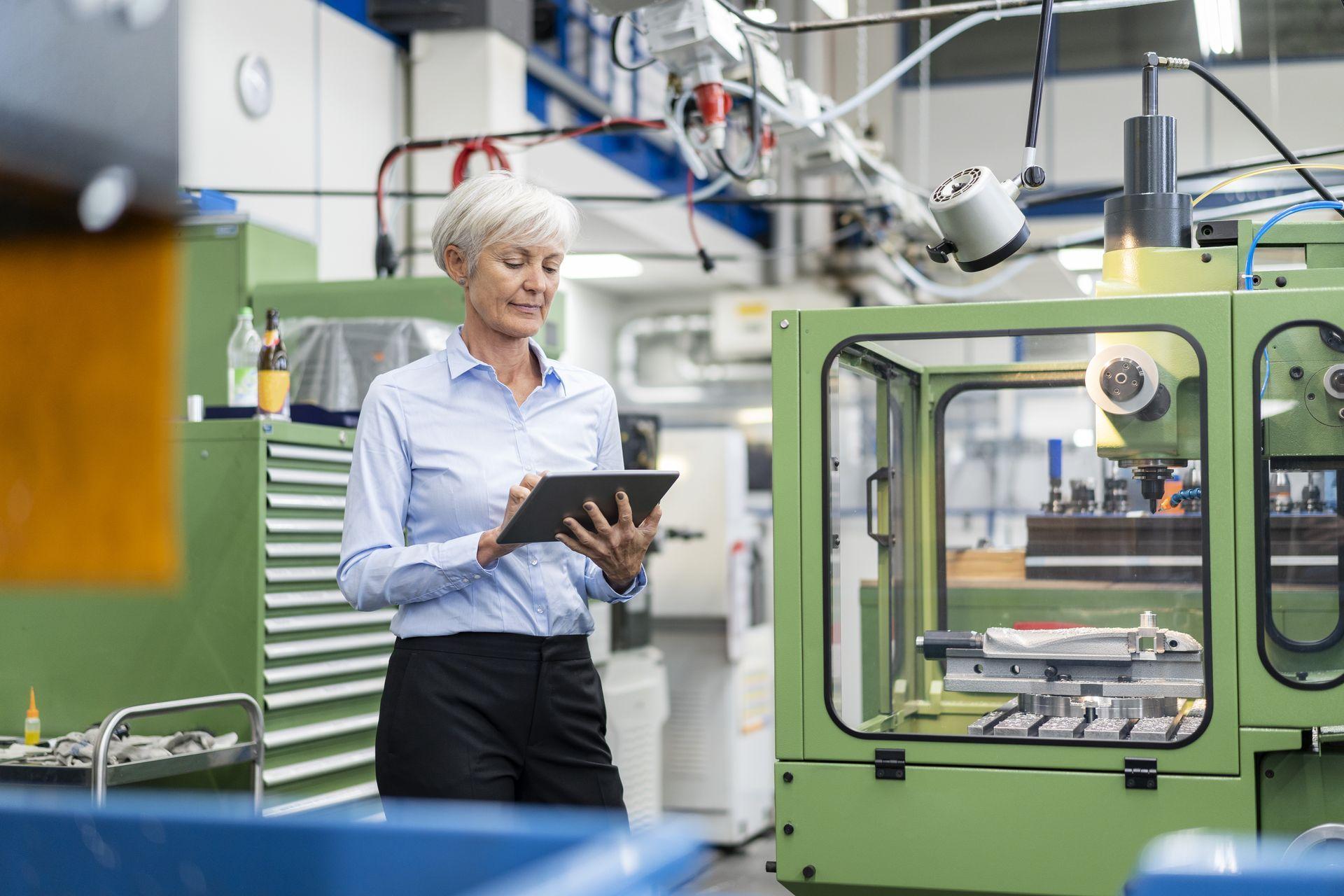
Lights out, dark factory
The term “Dark Factory” (also known as Lights Out Manufacturing) refers to an industrial production facility that is entirely automated, allowing for manufacturing without direct human involvement at the site. From beginning to end, the entire manufacturing process is carried out by automatically controlled machinery. The term alludes to the fact that a facility in which no individuals are employed that need light for their jobs could theoretically be carried out without illumination, in the dark.
Even with the most sophisticated automation, certain tasks still need human attention or, in some cases, the ability to perform them. As a result, some of these factories are only partly automated for periods, such as during particular shifts.
The notion that all manufacturing processes can be fully automated solely according to pre-programmed and established procedures in the dark is a metaphor. In reality, Artificial Intelligence in Industry 4.0 needs to see too. Robotic manufacturing in total darkness is feasible only if the equipment does not employ any optical sensors and no visual monitoring by humans is utilized.